APQP
- ftunin
- 14 de mai. de 2020
- 27 min de leitura
Planejamento Avançado da Qualidade do Produto

1 Introdução
A finalidade do APQP é comunicar às organizações (internas e externas) e fornecedores as diretrizes comuns do Planejamento da Qualidade do Produto e Plano de Controle desenvolvidas em conjunto pela Chrysler, Ford e General Motors. O manual apresenta diretrizes designadas para produzir um plano de qualidade do produto que dê suporte ao desenvolvimento de um produto ou serviço que trará satisfação ao cliente. Alguns dos benefícios esperados ao adotar essas diretrizes incluem:
· Uma redução na complexidade do planejamento da qualidade do produto para o cliente e organizações.
· Um meio para as organizações comunicarem com facilidade os requisitos do planejamento da qualidade do produto aos fornecedores.
O APQP contém diretrizes que dão suporte aos requisitos descritos na ISO/TS 16949 e aos requisitos aplicáveis específicos do cliente.
Ciclo de Planejamento da Qualidade de Produto


O Ciclo de Planejamento da Qualidade de Produto ao lado é uma representação de um programa típico. As várias fases são mostradas sequencialmente para representar o cronograma planejado para executar as funções descritas,
A finalidade:
· O planejamento avançado. Os primeiros três quartos do ciclo são desenvolvidos para o planejamento prévio da qualidade do produto através da validação do produto/processo.
· ato de implementação. O último quarto é o estágio em que a importância da avaliação dos resultados tem duas funções: determinar se os clientes estão satisfeitos e dar suporte à busca pela melhoria contínua.
A representação do planejamento da qualidade do produto como um ciclo ilustra a busca interminável pela melhoria contínua que somente pode ser alcançada adquirindo experiência em um programa e aplicando o conhecimento absorvido no programa subsequente.
Matriz de Responsabilidade do Planejamento da Qualidade do Produto
A matriz abaixo representa as Funções do Planejamento da Qualidade do Produto para três tipos de organizações. Sua função é ajudar as organizações a definirem a abrangência de suas responsabilidades de planejamento. A matriz não representa todos os diferentes tipos de relações do planejamento da qualidade do produto que podem existir entre as organizações, fornecedores e clientes.

1.1 Princípios do Planejamento da Qualidade do Produto
O Planejamento da Qualidade do Produto é um método estruturado para definir e estabelecer as etapas necessárias para garantir que um produto satisfaça o cliente. A meta do planejamento da qualidade do
produto é facilitar a comunicação com todos os envolvidos para assegurar que todas as etapas necessárias sejam completadas dentro do prazo. Um planejamento efetivo da qualidade do produto depende do compromisso da alta gerência da empresa em relação ao esforço necessário para atingir a satisfação do cliente. Alguns dos benefícios do planejamento da qualidade do produto incluem:
· Direcionar recursos para satisfazer o cliente.
· Promover a identificação antecipada das alterações necessárias.
· Evitar alterações de última hora.
· Fornecer um produto de qualidade dentro do prazo a um custo reduzido.
1.1.1 Organizar a Equipe
O primeiro passo é determinar um responsável pelo projeto APQP. Além disso uma equipe multifuncional deveria ser estabelecida para assegurar um planejamento efetivo da qualidade do produto. A equipe deveria incluir representantes de diferentes funções, tais como, engenharia, manufatura, controle de material, compras, qualidade, recursos humanos, vendas, assistência técnica, fornecedores e clientes, conforme apropriado.
1.1.2 Definir a Abrangência
É importante que a equipe de planejamento da qualidade do produto da organização identifique, no estágio inicial do programa, as necessidades, expectativas e requisitos dos clientes. No mínimo a equipe deve se reunir para:
· Selecionar um líder de equipe do projeto responsável pela supervisão do processo de planejamento.
· Definir os papéis e a responsabilidade de cada área representada.
· Identificar os clientes - internos e externos.
· Definir os requisitos dos clientes.
· Selecionar as disciplinas, indivíduos e/ou fornecedores que devem se juntar à equipe, e aqueles que não são necessários.
· Compreender as expectativas dos clientes, ou seja, o projeto, número de testes.
· Avaliar a viabilidade do projeto proposto, requisitos de desempenho e processo de manufatura.
· Identificar os custos, cronograma e restrições que devem ser considerados.
· Determinar a assistência exigida por parte do cliente.
· Identificar o processo ou método de documentação.
1.1.3 Equipe a Equipe
A equipe de planejamento da qualidade do produto da organização deve estabelecer as linhas de comunicação com outros clientes e com as equipes de outras empresas. Isto pode incluir reuniões periódicas com outras equipes. A extensão do contato equipe a equipe depende do número de pendências que requerem solução.
1.1.4 Treinamento
O sucesso de um Plano da Qualidade do Produto depende de um programa de treinamento efetivo que comunique todos os requisitos e habilidades de desenvolvimento para atender ás necessidades e expectativas do cliente.
1.1.5 Envolvimento do Cliente e da Organização
O cliente principal pode iniciar o processo de planejamento da qualidade com uma organização. No entanto, a organização tem a obrigação de estabelecer uma equipe multifuncional para gerenciar o processo de planejamento da qualidade do produto. As organizações devem esperar o mesmo desempenho dos seus fornecedores.
1.1.6 Engenharia Simultânea
Engenharia simultânea é um processo no qual as equipes multifuncionais buscam um objetivo comum. Ela substitui a série sequencial de fases em que os resultados são transmitidos para a próxima área para que sejam executados. Sua finalidade é agilizar a introdução de produtos com qualidade em menos tempo. A equipe de planejamento da qualidade do produto da organização assegura que outras áreas e equipes planejem e executem atividades que deem suporte ao objetivo ou objetivos comuns.
1.1.7 Planos de Controle
Planos de controle são descrições por escrito dos sistemas de controle de peças e processos. Os planos de controle específicos englobam três fases distintas:
· Protótipo - Uma descrição das medições dimensionais e testes de material e desempenho que ocorrerão durante a construção do protótipo.
· Pré-Lançamento - Uma descrição das medições dimensionais e testes de material e desempenho que ocorrerão após a construção do protótipo antes de produção em série.
· Produção - Uma documentação abrangente das características do produto/processo, controles de processo, testes e sistemas de medição ocorrerão durante a produção em série.
1.1.8 Resolução de Problemas
Durante o processo de planejamento, a equipe encontrará problemas com o projeto e/ou processo do produto. Esses problemas deveriam ser documentados numa matriz com a designação de responsabilidades e um cronograma de resolução. Métodos disciplinados de resolução de problemas são recomendados em situações difíceis.
1.1.9 Planos Referentes ao Cronograma
O sucesso de qualquer programa depende do atendimento das necessidades e expectativas do cliente no prazo adequado com custo que represente valor. O Cronograma de Planejamento da Qualidade do Produto e o Ciclo de Planejamento da Qualidade do Produto requerem que a equipe de planejamento concentre seus esforços na prevenção de problemas, que é dirigida pela Engenharia Simultânea e efetuada pelas atividades de engenharia do produto e manufatura que trabalham simultaneamente. As equipes de planejamento devem estar preparadas para modificar os planos da qualidade do produto a fim de atender às expectativas do cliente. A equipe de planejamento da qualidade do produto da organização é responsável por assegurar que o cronograma atenda ou supere o cronograma do cliente
Cronograma de Planejamento da Qualidade do Produto
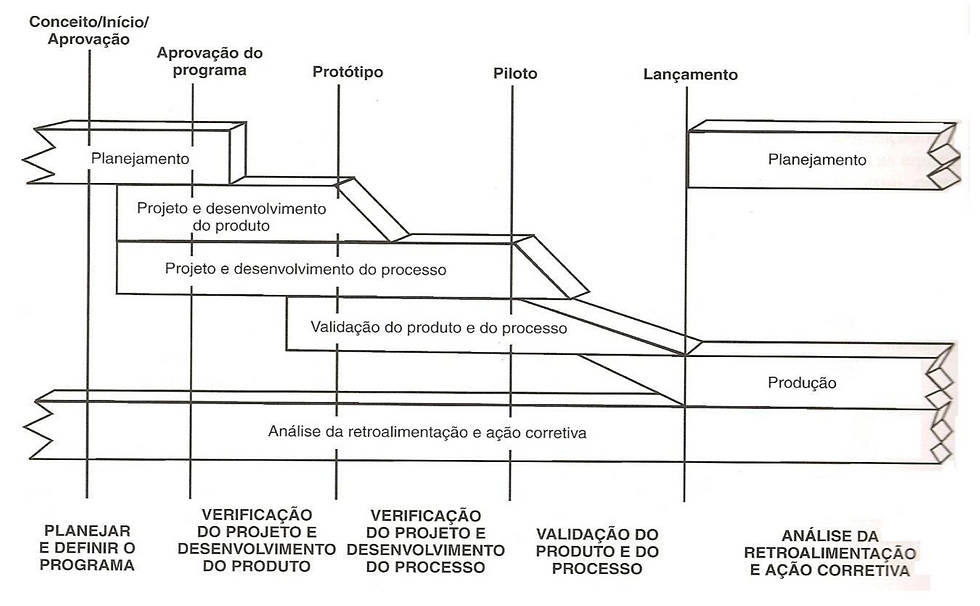
2 Planejar e Definir o Programa
A meta de qualquer programa de produto é atender às necessidades do cliente e proporcionar, simultaneamente, um valor competitivo. O estágio inicial do processo de planejamento da qualidade do produto é assegurar que as necessidades e expectativas do cliente sejam claramente compreendidas.
Os inputs e outputs aplicáveis ao processo de planejamento podem variar de acordo com o processo de desenvolvimento do produto e com as necessidades e expectativas do cliente. Algumas recomendações são mostradas a seguir:
2.1 Voz do Cliente
A “Voz do Cliente” engloba reclamações, recomendações, dados e informações obtidas de cliente interno
e/ou externos. Alguns métodos para obter essas informações são:
2.1.1 Pesquisa de Mercado
A equipe de planejamento da qualidade do produto da organização pode necessitar dos dados e informações de pesquisas de mercado que reflitam a Voz do Cliente. Algumas fontes podem auxiliar na identificação das preocupações e desejos do cliente e traduzir essas preocupações em características do produto e processo:
· Entrevistas com clientes;
· Questionários e pesquisas junto aos clientes;
· Teste de mercado e relatórios de posicionamentos de mercado;
· Estudos de qualidade e confiabilidade de novos produtos;
· Estudos de qualidade do produto da concorrência;
· Melhores Práticas;
· Lições Aprendidas.
2.1.2 Informações Históricas de Garantia e Qualidade
Uma lista de informações históricas sobre as preocupações e desejos do cliente deveria ser preparada para avaliar o potencial de recorrência durante o projeto, manufatura, instalação e uso do produto. Estes dados deveriam ser considerados uma extensão dos outros requisitos de projeto e devem ser incluídos na análise das necessidades do cliente.
Muitos dos itens abaixo podem ajudar a equipe a identificar as preocupações e desejos do cliente e priorizar as resoluções apropriadas.
· Melhores Práticas;
· Lições Aprendidas;
· Relatórios de garantia;
· Índices de capabilidade;
· Relatórios de qualidade interna da planta do fornecedor;
· Relatórios de resolução de problemas;
· Retorno e rejeições da planta pelo cliente;
· Análise de produto retornado do campo.
2.1.3 Experiência da Equipe
A equipe pode usar qualquer fonte de informação, conforme apropriado, incluindo as seguintes:
· Inputs de nível de sistemas superiores ou projetos de Desdobramento da Função da Qualidade
· (QFD);
· Comentários e análises da mídia: reportagens de revistas e jornais, etc.;
· Cartas e sugestões de clientes;
· Melhores Práticas;
· Lições Aprendidas;
· Comentários de concessionários;
· Comentários de Operadores de Frota;
· Relatórios de serviços e assistências técnica;
· Avaliações internas usando clientes substitutos;
· Testes de rodagem;
· Comentários ou diretrizes de gerência;
· Problemas e pontos de vista relatados por clientes internos;
· Requisitos e normas governamentais;
· Revisão de contrato.
2.2 Plano de Negócios e Estratégias de Marketing
O plano de negócios e estratégias de marketing do cliente determinarão os moldes do plano da qualidade do produto. O plano de negócios pode impor restrições à equipe (por exemplo, prazo, custo, investimento, posicionamento do produto, recursos de pesquisas e desenvolvimento (P&D) que alteram o tomado. A estratégia de marketing definirá o cliente-alvo, os principais pontos de vendo e principais concorrentes.
2.3 Dados de Benchmark do Produto/Processo
O uso de benchmark fornecerá o input para estabelecer as metas de desempenho do produto/processo. A pesquisa e desenvolvimento também podem fornecer benchmarks e idéias conceituais. Um método para fazer benchmarketing de forma bem sucedida é:
· Identificar os benchmarks apropriados;
· Compreender o motivo da diferença entre a situação atual e o benchmark;
· Desenvolver um plano para diminuir a diferença com o benchmark. Equiparar-se a ele ou excedê-lo.
2.4 Premissas do Produto/Processo
Haverá premissas de que o produto possui certas características, conceitos de projeto e processo. Isso inclui inovações técnicas, materiais avançados, avaliações de confiabilidade e novas tecnologias. Todos estes elementos deveriam ser utilizados como inputs.
2.5 Estudos de Confiabilidade do Produto
Este tipo de dado considera a freqüência de reparos ou substituições de componentes dentro de determinados períodos e os resultados dos testes de confiabilidades/durabilidade de longo prazo.
2.6 Inputs do Cliente
Os futuros usuários do produto podem fornecer informações valiosas relacionadas à suas necessidades e expectativas. Além disso, os futuros usuários do produto já podem ter realizado algumas ou todas as revisões e estudos mencionados anteriormente. Esses inputs deveriam ser usados pelo cliente e/ou organização para desenvolver medidas acordadas de satisfação do cliente.
2.7 Objetivos do Projeto
Os objetivos do projeto são uma tradução da Voz do Cliente em objetivos de projeto mensuráveis. A seleção adequada dos objetivos do projeto assegura que a Voz do Cliente não seja perdida nas atividades subseqüentes do projeto. A Voz do Cliente também inclui requisitos reguladores, tais como relatórios de composição de materiais e fabricação de peças poliméricas.
2.8 Metas de Confiabilidade e Qualidade
As metas de confiabilidade são estabelecidas com base nos desejos e expectativas do cliente, objetivos do programa e benchmarks de confiabilidade. Um exemplo dos desejos e expectativas do cliente pode ser
nenhuma falha de segurança. Alguns benchmarks de confiabilidade podem ser a confiabilidade do produto da concorrência, dados de garantia ou frequência de reparos num determinado período de tempo. As metas de qualidade deveriam ser baseadas na melhoria contínua como, por exemplo, parte por milhão, níveis de defeito ou redução de refugos.
2.9 Lista Preliminar de Materiais
A equipe deveria estabelecer uma lista preliminar de materiais baseada nas premissas do produto/processo e incluir uma lista de fornecedores potenciais. Para identificar as características preliminares especiais do produto/processo, é necessário que o projeto e processo de manufatura adequados tenham sido selecionados.
2.10 Fluxograma Preliminar do Processo
· processo de manufatura antecipado deveria ser descrito através de um fluxograma de processo desenvolvido a partir da lista preliminar de materiais e das premissas do produto/processo.
2.11 Identificação Preliminar das Características Especiais do Produto e Processo
As características especiais do produto e processo são identificadas pelo cliente, além das selecionadas pela organização através do conhecimento do produto e processo. Alguns exemplos de inputs para identificação das características especiais incluem:
· Premissas do produto baseadas na análise das necessidades e expectativas do cliente;
· Identificação das metas e requisitos de confiabilidade;
· Identificação das características especiais do processo a partir do processo de manufatura antecipado;
· FMEAs de peças similares.
2.12 Plano de Garantia do Produto
O Plano de Garantia do Produto traduz os objetivos do projeto em requisitos de projeto, baseado nas necessidades e expectativas do cliente. Este manual não prescreve um método específico para preparar um Plano de Garantia do Produto. O Plano de Garantia do Produto pode ser desenvolvido em qualquer formato conhecido pela organização e deveria incluir os seguintes itens:
· Descrição dos requisitos do programa;
· Identificação das metas e/ou requisitos de confiabilidade, durabilidade e sua distribuição/alocação;
· Avaliação dos requisitos de novas tecnologias,complexidade, materiais, aplicação, meio ambiente, embalagem, assistência técnica e manufatura, ou qualquer outro fator que possa colocar o programa em risco;
· Uso da FMEA;
· Desenvolvimento dos requisitos preliminares de engenharia.
2.13 Suporte da Gerência
Uma das chaves para o sucesso do Planejamento Avançado da Qualidade do Produto é o interesse, comprometimento e suporte da alta gerência. A participação da gerência nas reuniões de planejamento da qualidade do produto é vital para assegurar o sucesso do programa. A equipe deveria atualizar a gerência
na conclusão de cada fase do planejamento da qualidade do produto para reforçar o seu comprometimento e apoio. Atualizações e/ou solicitações de ajuda podem ocorrer com mais frequência, conforme necessário. Uma das metas principais do Planejamento Avançado da Qualidade do Produto é manter o suporte da gerência através da demonstração de que todos os requisitos do planejamento foram atendidos e/ou os problemas foram documentados ou programados para resolução, incluindo um cronograma do programa e um planejamento de recursos e pessoal para dar sustentação à capacidade necessária.
3 Projeto e Desenvolvimento do Produto
Todos os fatores do projeto deveriam ser considerados pela organização no processo de Planejamento Avançado da Qualidade do Produto, mesmo que o projeto pertença ao cliente ou seja compartilhado. As etapas incluem a construção do protótipo para verificar se o produto ou serviço atinge os objetivos da Voz do Cliente. Um projeto viável deve permitir que os volumes e programação de produção sejam atendidos, e ser consistente com a habilidade em atender aos requisitos de engenharia, juntamente com os objetivos da qualidade, confiabilidade, custos de investimento, peso, custo por unidade e prazos. Embora os estudos de viabilidade e planos de controle sejam principalmente baseados nos requisitos dos desenhos de engenharia e especificações, informações valiosas podem ser obtidas a partir de ferramentas analíticas aqui descritas para definir melhor e priorizar as características que podem requerer controles especiais do produto e processo.
Neste estágio do processo, uma análise preliminar de viabilidade será feita para avaliar os problemas potenciais que podem ocorrer durante a manufatura.
Os inputs e outputs são:
3.1 Análise de FMEA
A DFMEA é uma técnica analítica disciplinada que avalia a probabilidade de uma falha, bem como o efeito de tal falha. A DFMEA é um documento vivo continuamente atualizado de acordo com as necessidades e expectativas do cliente. Ela é um input importante para o processo APQP que pode incluir as características do produto e processo previamente selecionadas.
3.2 Projeto para Manufaturabilidade e Montagem
O projeto para Manufaturabilidade e Montagem é um processo de Engenharia Simultânea idealizado para otimizar a relação entra a função do projeto, manufatura e facilidade de montagem. A abrangência das necessidades e expectativas do cliente, definidas anteriormente, determinará a extensão do envolvimento da equipe de planejamento da qualidade do produto da organização nesta atividade. No mínimo, os itens a seguir deveriam ser considerados pela equipe de planejamento da qualidade do produto da organização:
· Projeto, conceito, função e sensibilidade à variação de manufatura;
· Processo de manufatura e/ou montagem;
· Tolerâncias dimensionais; Requisitos de desempenho;
· Número de componentes;
· Ajustes do processo;
· Manuseio de material.
3.3 Verificação do Projeto
A verificação do projeto verifica se o projeto do produto atende aos requisitos do cliente derivados das atividades descrita no capítulo anterior.
3.4 Análises Críticas do Projeto
As análises críticas do projeto são reuniões periodicamente agendadas conduzidas pela engenharia de projeto da organização e devem incluir as outras áreas afetadas. A análise crítica do projeto é um método efetivo para prevenir problemas e mal-entendidos; ela também fornece um mecanismo para monitorar o andamento, relatar à gerência e obter a aprovação do cliente, conforme necessário.
As análises críticas de projeto são uma série de atividades de verificação que vão além de uma simples engenharia. No mínimo, as revisões de projeto deveriam incluir uma avaliação do(s)/da(s):
· Considerações sobre o(s) requisito(s) do Projeto/Funcional(ais);
· Metas formais de confiabilidade e confiança;
· Ciclos de rendimento dos componentes/subsistemas/sistemas;
· Resultados de simulações por computador e de testes de bancada;
· DFMEA(s);
· Análise crítica dos esforços do Projeto para Manufaturabilidade e Montagem;
· Resultados do Delineamento de Experimentos (DOE) e da variação da montagem do conjunto;
· Falhas de teste;
· Progresso da verificação do projeto.
A principal função das análises críticas do projeto é acompanhar o progresso da verificação do projeto. A organização deveria acompanhar o progresso da verificação do projeto através do uso de um formulário de planejamento e relatório, conhecido por alguns clientes como Plano e Relatório de Verificação do Projeto (DVP&R). o plano e o relatório são um método formal para assegurar a:
· Verificação do projeto;
· Validação do produto e processo de componentes e conjuntos através da aplicação de um amplo planejamento e relatórios de testes.
A equipe de planejamento da qualidade do produto da organização não deve se limitar aos itens listados acima.
3.5 Construção do Protótipo - Plano de Controle
Os planos de controle do Protótipo são uma descrição das medições dimensionais e testes de material e de funcionamento que ocorrerão durante a construção do Protótipo. A equipe de planejamento da qualidade do produto da organização deveria assegurar que um plano de controle do protótipo seja preparado.
A manufatura das peças do protótipo é uma excelente oportunidade para a equipe e o cliente avaliarem o quanto o produto ou serviço atinge os objetivos da Voz do Cliente. É responsabilidade da equipe de planejamento da qualidade do produto da organização analisar criticamente os protótipos para:
· Assegurar que o produto ou serviço atenda às especificações a aos dados registrados no relatório, conforme necessário;
· Assegurar que seja dada atenção específica às características especiais do produto e processo;
· Usar dados e experiência para estabelecer os parâmetros do processo preliminar e requisitos de embalagem;
· Comunicar ao cliente quaisquer preocupações, desvio e/ou impactos no custo.
3.6 Desenhos de Engenharia (Incluindo Modelos Matemáticos)
Os projeto do cliente não isentam a equipe de planejamento da qualidade do produto da organização da responsabilidade de analisar criticamente os desenhos de engenharia da maneira descrita a seguir. Os desenhos de engenharia podem incluir as características especiais (normas governamentais e de segurança) que devem ser descritas no plano de controle. Quando não existirem desenhos de engenharia do cliente, os desenhos de controle deveriam ser analisados criticamente pela equipe para determinar quais características afetam o ajuste, a função, a durabilidade e/ou os requisitos de segurança e normas governamentais.
Os desenhos deveriam ser analisados criticamente para determinar se há informações suficientes para o layout dimensional das peças individuais. As superfícies/pontos de controle ou referência deveriam ser claramente identificados de forma que dispositivos de medição funcionais e equipamentos apropriados possam ser projetados para controles contínuos. As dimensões deveriam ser avaliadas para assegurar a viabilidade e compatibilidade com os padrões de fabricação e medição. Se apropriado, a equipe deveria assegurar que os dados matemáticos sejam compatíveis com o sistema do cliente para uma comunicação mútua eficiente.
3.7 Especificações de Engenharia
Uma análise crítica detalhada e a compreensão das especificações de controle ajudarão a equipe de planejamento da qualidade do produto da organização a identificar os requisitos funcionais, de durabilidade e de aparência do componente ou conjunto em questão. O tamanho da amostra, a frequência e os critérios de aceitação destes parâmetros são normalmente definidos na seção de teste em processo da Especificação de Engenharia. Caso contrário, o tamanho da amostra e a frequência devem ser determinados pela organização e relacionados no plano de controle. Em ambos os casos, a organização deveria determinar quais características afetam o atendimento aos requisitos funcionais, de durabilidade e de aparência.
3.8 Especificações de Material
Além dos desenhos e das especificações de desempenho, as especificações de material deveriam ser analisadas criticamente quanto às características especiais relacionadas aos requisitos de propriedades físicas, de desempenho, ambientais, de manuseio e de estocagem. Essas características também deveriam ser incluídas no plano de controle.
3.9 Alterações de Desenhos e Especificações
Quando forem necessárias alterações de desenhos e especificações, a equipe deve assegurar que essas alterações sejam prontamente comunicadas e adequadamente documentadas para todas as áreas afetadas.
3.10 Requisitos para Novos Equipamentos, Ferramental e Instalações
A DFMEA, o Plano de Garantia do produto e/ou as análises críticas do projeto podem identificar a necessidade de novos equipamentos e instalações, incluindo o atendimento aos requisitos de capacidade. A equipe de planejamento da qualidade do produto da organização deveria contemplar esses requisitos adicionando os itens ao Cronograma. A equipe deveria assegurar que haja um processo para determinar que o novo equipamento e ferramental sejam apropriados e entregues no tempo oportuno. O progresso das instalações deveria ser monitorado para assegurar sua conclusão antes da data planejada para o “tryout” de produção.
3.11 Características Especiais do Produto e Processo
No estágio “Planejar e Definir o Programa), a equipe identificou as características especiais preliminares do produto e processo. A equipe de planejamento da qualidade do produto da organização deveria basear- se nesta lista e atingir um consenso através da avaliação das informações técnicas. A organização deveria consultar os requisitos específicos do cliente para detalhes adicionais sobre o uso das características especiais do produto e processo. O consenso deve ser documentado no plano de controle apropriado. Os formulários de Características Especiais do plano de Controle e Coordenadas de Pontos de Dados, são métodos recomendados para documentar e atualizar as características especiais. A organização pode usar qualquer formulário que atenda aos requisitos de documentação.
3.12 Requisitos para Dispositivos de Medição / Equipamento de Teste
Os requisitos para dispositivos de medição/equipamentos de teste também podem ser identificados nesta etapa. A equipe de planejamento da qualidade do produto da organização deveria adicionar esses requisitos ao Cronograma. O progresso deveria ser monitorado para assegurar que o prazo necessário seja atendido.
3.13 Comprometimento da Equipe com a Viabilidade e Suporte da Gerência
A equipe de planejamento da qualidade do produto da organização deve avaliar a viabilidade do projeto proposto nesta fase. A propriedade do projeto por parte do cliente não exclui a obrigação da organização de avaliar a viabilidade do projeto. A equipe deve estar convencida de que o projeto proposto pode ser manufaturado, montado, testado, embalado e entregue na quantidade suficiente e dentro do prazo, com um custo aceitável para o cliente. O consenso da equipe de que o projeto proposto é viável deveria ser documentado juntamente com todas as questões em aberto que requerem uma resolução e apresentado à gerência para obter o seu suporte.
4 Projeto e Desenvolvimento do Processo
As tarefas a serem realizadas nesta etapa do processo de planejamento da qualidade do produto dependem da conclusão bem-sucedida dos estágios anteriores. O sistema de manufatura deve assegurar que os requisitos, necessidades e expectativas do cliente sejam atendidos. Os inputs e outputs aplicáveis a essa etapa do processo são:
4.1 Padrões e Especificações de Embalagem
O cliente normalmente terá requisitos de embalagem que deveriam ser incorporados em todas as especificações de embalagem para o produto. Se nenhum requisito for fornecido, o projeto da embalagem deveria assegurar a integridade do produto até o seu uso. A equipe de planejamento da qualidade do produto da organização deveria assegurar que a embalagem individual (incluindo divisões internas) de um produto seja projetada e desenvolvida. Os padrões de embalagem do cliente ou os requisitos genéricos de embalagem deveriam ser adotados, quando apropriado. Em todos os casos, o projeto da embalagem deveria assegurar que o desempenho e as características do produto permaneçam inalterados durante os processos de embalagem, transporte e desembalagem. A embalagem deveria ser compatível com todos os equipamentos de manuseio de material identificados, incluindo robôs.
4.2 Análise Crítica do Sistema da Qualidade do Produto/Processo
A equipe de planejamento da qualidade do produto da organização deveria analisar criticamente o Sistema de Gerenciamento da Qualidade no local de manufatura. Todos os controles adicionais e/ou alterações necessárias de procedimento para produzir o produto deveriam estar atualizados, documentados e incluídos no plano de controle de manufatura. Esta é uma oportunidade para a equipe de planejamento da qualidade do produto da organização aprimorar o sistema da qualidade existente com base nos inputs do cliente, habilidade da equipe e experiência anterior.
4.3 Fluxograma do Processo
O fluxograma do processo é uma esquematização do fluxo atual ou proposto do processo. Ele pode ser utilizado para analisar as fontes de variação de máquinas, materiais, métodos e mão-de-obra do começo ao fim do processo de manufatura ou montagem. Ele é utilizado para enfatizar o impacto das fontes de variação sobre o processo. O fluxograma ajuda a analisar o processo como um todo e não suas etapas individuais. O fluxograma auxilia a equipe de planejamento da qualidade do produto da organização a direcionar o foco no processo, ao conduzir a PFMEA e idealizar o Plano de Controle. A Lista de Verificação do Fluxograma pode ser usada pela equipe de planejamento da qualidade do produto da organização para ajudar nesta avaliação.
4.4 Layout das Instalações
As instalações deveriam ser desenvolvidas e analisadas criticamente para determinar a aceitabilidade de importantes itens de controle, aplicabilidade de recursos visuais, áreas de trabalhos interinas e áreas de estocagem para material não - conforme. Todo o fluxo de material deveria ser adaptado ao fluxograma do processo e plano de controle. A Lista de Verificação das Instalações pode ser usada pela equipe de planejamento da qualidade do produto da organização para ajudá-la nesta avaliação. O layout das instalações deveria ser desenvolvido de forma a otimizar a movimentação e manuseio de material e a utilização com valor agregado das instalações, e deveria facilitar o fluxo sincronizado dos materiais através do processo.
4.5 Matriz de Características
Uma matriz de características é uma técnica analítica recomendada para mostrar a relação entre os parâmetros do processo e as estações de manufatura.
4.6 Análise de Modo e Efeitos de Falha de Processo (PFMEA)
A PFMEA deveria ser conduzida durante o planejamento da qualidade do produto e antes do início da produção. É uma análise e revisão disciplinadas, de processos novos ou revisados que é efetuada para antecipar, solucionar ou monitorar problemas de processo em potencial para o programa de um produto novo ou revisado. A Lista de Verificação de FMEA de Processo pode ser usada pela equipe de planejamento da qualidade do produto da organização para ajudar nesta avaliação.
4.7 Plano de Controle de Pré-Lançamento
Os Planos de Controle de Pré-Lançamentos são descrições das medições dimensionais e dos testes de material e funcional que irão ocorrer após o protótipo e antes da produção em série. O plano de controle de pré-lançamento deveria incluir controles adicionais de produto/processo a serem implementados até o processo de produção ser validado. O propósito do plano de controle de pré-lançamento é controlar não – conformidades em potencial durante, ou antes, da produção inicial. Alguns exemplos de aprimoramentos do plano de controle de pré-lançamento incluem:
· Inspeções mais freqüentes;
· Mais itens de verificação durante e no final do processo;
· Avaliações estatísticas práticas; Auditorias aprimoradas;
· Identificação de meios para efetuar a prova de erro.
A Lista de Verificação do Plano de Controle pode ser usada pela equipe de planejamento da qualidade do produto da organização para ajudar nesta avaliação.
4.8 Instruções de Processo
A equipe de planejamento da qualidade do produto da organização deveria assegurar que as instruções do processo proporcionem a compreensão adequada e detalhes suficientes para todo o pessoal que tenha responsabilidade direta com o funcionamento dos processos. Essas instruções deveriam ser desenvolvidas a partir das seguintes fontes:
· FMEAs;
· Plano(s) de controle;
· Desenhos de engenharia, especificações de desempenho, especificações de material, padrões visuais e normas industriais;
· Fluxograma do processo;
· Layout das instalações;
· Matriz de características;
· Padrões e Especificações de Embalagem;
· Parâmetros de processo;
· Especialização e conhecimento dos processos e produtos por parte da organização;
· Requisitos de manuseio;
· Operadores do processo.
As instruções do processo para os procedimentos-padrão de operação deveriam ser divulgadas e incluir parâmetros de ajuste, tais como: velocidade das máquinas, alimentadores, tempos dos ciclos e ferramental, e deveriam estar acessíveis aos operadores e supervisores. Informações adicionais sobre a preparação das instruções do processo podem ser encontradas nos requisitos específicos do cliente apropriado.
4.9 Plano de Análise dos Sistemas de Medição
A equipe de planejamento da qualidade do produto da organização deveria assegurar que seja desenvolvido um plano que efetue a análise dos sistemas de medição requeridos, incluindo recursos para a verificação. Esse plano deveria incluir, no mínimo, um escopo apropriado do laboratório para as medições e testes necessários, a responsabilidade de assegurar a linearidade, precisão, repetitividade e reprodutibilidade dos dispositivos de medição, e a correlação entre dispositivos duplicados.
4.10 Plano de Estudo preliminar de Capabilidade do Processo
A equipe de planejamento da qualidade do produto da organização deveria assegurar o desenvolvimento de um plano preliminar de capabilidade do processo. As características identificadas no plano preliminar de capabilidade do processo. As características identificadas no plano de controle servirão como base para o plano de estudo preliminar de capabilidade do processo.
4.11 Suporte da Gerência
A equipe de planejamento da qualidade do produto da organização deveria programar uma análise crítica formal idealizada para reforçar o comprometimento da gerência na conclusão da fase de projeto e
desenvolvimento do processo. Essa análise é fundamental para manter a alta gerência informada e obter o seu apoio para auxiliar nas soluções de quaisquer assuntos em aberto. O suporte da gerência inclui a confirmação do planejamento e o fornecimento de recursos e pessoal para atender à capacidade requerida.
5 Validação do Produto e Processo
Durante uma corrida piloto de produção, a equipe de planejamento da qualidade do produto deveria assegurar que o plano de controle e o fluxograma do processo estejam sendo seuidos, e que os produtos atendam aos requisitos do cliente. Assuntos adicionais deveriam ser identificados para investigação e resolução antes do início da produção regular.
Os inputs e outputs às etapas do processo são:
5.1 Corrida Piloto de Produção
A corrida piloto de produção deve ser conduzida usando-se o ferramental de produção, equipamentos de produção, ambiente de produção (incluindo operadores de produção), instalações, dispositivos de medição da produção e taxa de produção. A validação da efetividade do processo de manufatura começa com a corrida piloto de produção. Normalmente, a quantidade mínima para uma corrida piloto de produção é estabelecida pelo cliente, mas ela pode ser excedida pela equipe de planejamento da qualidade do produto da organização.
Os outputs da corrida piloto de produção (produto) são usados para: Estudo preliminar de capabilidade do processo;
· Análise dos sistemas de medição;
· Demonstração da taxa de produção;
· Revisão do processo;
· Testes de validação da produção;
· Aprovação de peça de produção;
· Avaliação da embalagem;
· “First Time Capability” (FTC);
· Aprovação do planejamento da qualidade;
· Amostras de peças de produção;
· Amostra mestre (conforme necessário).
5.2 Análise dos Sistemas de Medição
Os dispositivos e métodos de monitoramento e medição especificados deveriam ser utilizados para verificar as características identificadas no plano de controle em relação às especificações de engenharia, devendo ser submetidos a uma avaliação dos sistemas de medição durante ou antes da corrida piloto de produção.
5.3 Estudo Preliminar de Capabilidade do Processo
O estudo preliminar de capabilidade do processo deveria se desenvolver com base nas características identificadas no plano de controle. O estudo fornece uma avaliação da prontidão do processo para produção.
5.4 Aprovação de Peça de Produção
O objetivo da aprovação de peça de produção é fornecer evidências de que todos os requisitos do registro do projeto de engenharia e requisitos de especificações do cliente sejam compreendidos de forma adequada pela organização e de que o processo de manufatura tem o potencial de produzir um produto consistente com tais requisitos durante a produção na taxa de produção cotada.
5.5 Teste de Validação da Produção
Os testes de validação da produção referem-se aos testes de engenharia que validam que os produtos manufaturados de acordo com os processo e ferramentas de produção atingem os padrões estabelecidos pela engenharia do cliente, incluindo os requisitos de aparência.
5.6 Avaliação de Embalagem
Todos os testes de embarque (quando necessário) e métodos de teste devem avaliar a proteção do produto contra danos durante o transporte e outros fatores adversos do ambiente. As embalagens especificadas pelo cliente não excluem o envolvimento da equipe de planejamento da qualidade do produto da organização em avaliar a eficiência da embalagem.
5.7 Plano de Controle de Produção
O plano de controle de produção é uma descrição por escrito dos sistemas para controlar peças e processos de produção. O plano de controle de produção é um documento vivo e deveria ser atualizado para refletir a adição/subtração de controles baseados na experiência adquirida em produzir peças. (Pode ser necessária a aprovação do representante autorizado do cliente). O plano de controle de produção é uma extensão lógica do plano de controle de pré-lançamento. A produção em série oferece á organização a oportunidade de avaliar os resultados, analisar criticamente o plano de controle e fazer as alterações necessárias.
5.8 Aprovação do planejamento da Qualidade e Suporte da Gerência
A equipe de planejamento da qualidade do produto da organização deveria fazer uma análise crítica no(s) local(is) de manufatura e coordenar uma aprovação formal. A aprovação da qualidade do produto indica à gerência que as atividades apropriadas do APQP foram concluídas. A aprovação ocorre antes da primeira expedição do produto e inclui uma análise crítica dos seguintes itens:
· Fluxogramas dos Processos. Verificar se os fluxogramas dos processos existem e se estão sendo seguidos.
· Planos de Controle. Verificar se os planos de controle existem, se estão disponíveis e se estão sendo seguidos o tempo todo para todas as operações afetadas.
· Instruções de Processo. Verificar se estes documentos contêm todas as características especiais especificadas no plano de controle e se todas as recomendações da PFMEA foram contempladas. Compare as instruções do processo, a PFMEA e o fluxograma do processo com plano de controle.
· Dispositivos de Monitoramento e Medição. Quando o plano de controle requisitar dispositivos de medição, acessórios ou equipamentos de teste especiais, verifique a repetitividade, a reprodutibilidade (GR&R) e o uso adequado do dispositivo.
· Demonstração da Capacidade Requerida. Uso dos processos, equipamento e pessoal de produção.
Após a conclusão da aprovação, uma análise critica deveria ser agendada com a gerência para informá-la sobre a situação do programa e obter o seu apoio para solucionar quaisquer questões em aberto. O
Sumário e Aprovação do planejamento da qualidade do produto são exemplos a documentação necessária para dar suporte a uma aprovação efetiva do planejamento da qualidade.
6 Retroalimentação, Avaliação e Ação Corretiva
O planejamento da qualidade não termina com a validação do processo e a instalação. É um estágio de manufatura de componente em que o resultado pode ser avaliado quando todas as causas comuns e especiais de variação estão presentes. Também é o momento de avaliar a efetividade dos esforços do planejamento da qualidade do produto. O plano de controles de produção é a base para avaliar o produto ou serviço nesse estágio. Dados variáveis e do tipo atributo devem ser avaliados. As organizações que implementarem integralmente um processo APQP efetivo estarão numa posição melhor para atender aos requisitos do cliente, incluindo as características especiais especificadas pelo cliente.
Os inputs e outputs aplicáveis à esta etapa do processo são:
6.1 Variação Reduzida
Deveriam ser adotadas cartas de controle e outras técnicas estatísticas como ferramentas para identificar a variação do processo. Análises deveriam ser feitas e ações corretivas deveriam ser adotadas para reduzir a variação. A melhoria contínua requer atenção não apenas das causas especiais de variação, mas também compreender as causas comuns e descobrir formas de reduzir estas fontes de variação.as propostas deveria ser desenvolvidas considerando0se os custos, o cronograma e a melhoria antecipada para revisão do cliente.
A redução ou eliminação de uma causa comum pode trazer benefício adicional de redução de custos. As organizações deveriam usar ferramentas, tais como análise de valor e redução de variação, para melhorar a qualidade e reduzir custos.
6.2 Maior Satisfação do Cliente
Atividades detalhadas de planejamento e a capabilidade demonstrada do processo de um produto ou serviço são componentes importantes da satisfação do cliente. No entanto, o produto ou serviço ainda deve se adequar ao ambiente do cliente. Este estágio de uso do produto requer a participação da organização. Nele tanto a organização como o cliente podem aprender muito. A efetividade dos esforços do planejamento da qualidade do produto pode ser avaliada nesse estágio.
A organização e o cliente devem ser parceiros para realizar as alterações necessárias a fim de corrigir quaisquer deficiências e aumentar a satisfação do cliente.
6.3 Entrega e Assistência Técnica
O estágio de entrega e assistência técnica do planejamento da qualidade mantém a parceria entre a organização e o cliente em relação à solução de problemas e melhoria contínua. As operações de substituição de peças e assistência técnica do cliente também dêem atender aos requisitos de qualidade, custo e entrega. A meta é atingir a qualidade na primeira vez. Entretanto, quando ocorrerem problemas ou deficiências no campo, é essencial que a organização e o cliente formem uma parceria efetiva para solucionar o problema e satisfazer o cliente final.
A experiência adquirida neste estágio fornece ao cliente e à organização o conhecimento necessário para reduzir os custos de processo, de inventário e de qualidade, e para fornecer o componente ou sistema certo para o próximo produto.
6.4 Uso Efetivo das Lições Aprendida/Melhores Práticas
Um portfólio das Lições Aprendidas ou Melhores Práticas é útil para capturar, reter e aplicar os conhecimentos. Os inputs para as Lições Aprendidas ou Melhores Práticas podem ser obtidos através de uma variedade de métodos, incluindo:
· Análise Crítica das “Coisas que Deram Certo/Coisas que Deram Errado”;
· Dados de garantia e outras medições de desempenho;
· Planos de ações corretivas;
· “Read-across” com produtos e processos similares;
· Estudos de DFMEA e PFMEA.
7 Metodologia do Plano de Controle
O objetivo da metodologia do plano de controle é ajudar a manufaturar produtos de qualidade de acordo com os requisitos do cliente. Isto é obtido apresentando-se uma abordagem estruturada para o projeto, seleção e implementação de métodos de controle que agregam valor ao sistema completo. Os planos de controle fornecem uma descrição resumida por escrito dos sistemas adotados para minimizar a variação do processo e do produto. O objetivo do formulário do plano de controle que será apresentado é fornecer um exemplo de como esta informação pode ser documentada. Um formulário alternativo pode ser usado, contanto que contenha, no mínimo, as mesmas informações. O plano de controle não substitui as informações contidas nas instruções detalhadas do operador. Essa metodologia é aplicável a uma ampla gama de processos e tecnologias de manufatura. O plano de controle é parte integral de um processo geral de qualidade e deve ser utilizado como um documento vivo. Por esse motivo, este capítulo deveria ser usado em conjunto com outros documentos afins.
Uma importante fase do processo do planejamento da qualidade é o desenvolvimento de um pano de controle. O plano de controle é uma descrição por escrito do sistema de controle das peça e processos.
Um único plano de controle pode se aplicar a um grupo ou família de produtos produzidos através do mesmo processo na mesma fonte. Se necessário, podem ser anexados esquemas e desenhos ao plano de controle para fins ilustrativos. Como suporte ao plano de controle, as instruções do operador e de monitoramento do processo deveriam ser definidas e usadas continuamente.
Na verdade, o plano de controle descreve as ações necessárias para cada fase do processo, incluindo o recebimento, o processo propriamente dito e seus resultados, e os requisitos periódicos para assegurar que todos os outputs do processo estejam sob controle. Durante as corridas regulares de produção, o plano de controle proporciona o monitoramento do processo e os métodos de controle que serão usados para controlar as características. Como os processo devem ser atualizados e melhorados continuamente, o plano de controle reflete uma estratégia sensível a estas condições de alteração do processo.
O plano de controle é mantido e usado durante todo o ciclo de vida do produto. No início do ciclo de vida do produto, seu primeiro objetivo é documentar e comunicar o plano inicial para o controle do processo. A seguir, ele guia a manufatura em como controlar o processo e assegurar a qualidade do produto. Finalmente, o plano de controle permanece como um documento vivo, refletindo os métodos de controle atuais e os sistemas de medição usados. O plano de controle é atualizado à medida que os sistemas de medição e os métodos de controle são avaliados e aprimorados.
Para que o controle e a melhoria do processo sejam eficazes, uma compreensão básica do processo deve ser adquirida. Uma equipe multidisciplinar é estabelecida para desenvolver o plano de controle usando todas as informações disponíveis para obter uma melhor compreensão do processo, tais como:
· Fluxograma do Processo;
· Análise de Modo e Efeitos de Falha de Sistema/Projeto/Processo;
· Características Especiais;
· Lições Aprendidas de Peças Similares;
· Conhecimento da Equipe em Relação ao Processo;
· Análise Crítica do Projeto;
· Métodos de Otimização (por exemplo, QFD, DOE, etc.)
Os benefícios do desenvolvimento e implementação de um plano de controle incluem:
Qualidade
A metodologia do plano de controle reduz os desperdícios e melhora a qualidade dos produtos durante o projeto, manufatura e montagem. Esta disciplina estruturada fornece uma avaliação completa do produto e do processo. Os planos de controle identificam as características do processo e os métodos de controle para as fontes de variação (variáveis de input) que causam variação nas características do produto (variáveis de output).
Satisfação do Cliente:
Os planos de controle direcionam os recursos para os processos e produtos relacionados às características que são importantes para o cliente. A alocação apropriada dos recursos neste itens principais ajuda a reduzir os custos sem prejudicar a qualidade.
Comunicação:
Como um documento vivo, o plano de controle identifica e comunica as alterações das características do produto/processo, do método de controle e da medição das características.
7.1 Descrição das Colunas do Plano de Controle

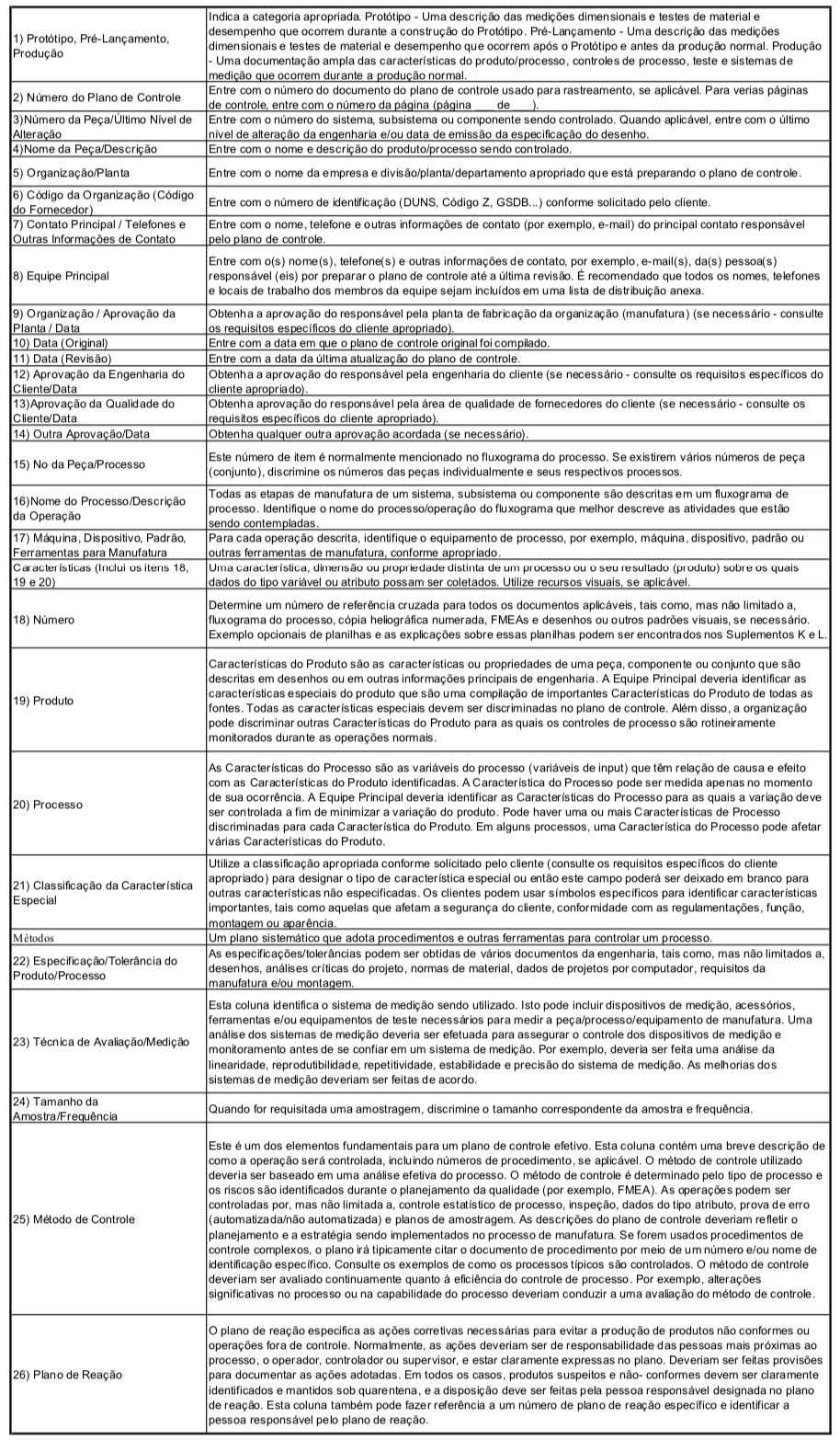
7.2 Análise do Processo
Tipos diferentes de processos apresentam desafios e oportunidades para controlar e reduzir a variação. Os tipos de processo podem estar relacionados a suas fontes mais comuns de variação ou seus fatores preponderantes na determinação da qualidade do produto. Existem muitos métodos efetivos para realizar a análise do processo. Cabe à organização determinar o melhor método para analisar o processo. Exemplos:
· Análise da Árvore de Falha
· Delineamento de Experimentos;
· Causa e Efeito.
Comments